Why “Good Enough” Solutions Are More Costly Than They Seem
We’ve all been there—facing a small problem and reaching for the quickest solution. Maybe it’s a Post-It note to mark inventory or a quick scribble in a notebook to track a delayed shipment. These kinds of ad hoc systems might seem like a quick fix at the time, but in reality, they’re creating invisible hidden costs that pile up and eat away at your bottom line.
The thing about “good enough” solutions is that, eventually, they aren’t. Sure, a sticky note works for a one-off task. But as your business grows and your processes get more complex, those little manual workarounds start to show their flaws. And when those flaws become too much to handle, you’re left dealing with inefficiencies, errors, and ultimately lost money.
They become one of those growing pains that start to hold you back as your business evolves and expands.
So, let’s take a closer look at the hidden costs of sticking with manual processes—and why an ERP system may just be the comprehensive solution you didn’t know you needed.
Time: The Silent Killer of Productivity
How many minutes a day do you or your team spend flipping through papers, looking for notes or files? Searching through stacks of paper for that one inventory count or sifting through emails to figure out what happened to that delayed order.
These little moments of disorganization might seem harmless on their own, but over time, they accumulate into a mountain of wasted hours. You might find yourself repeating manual tasks because a handwritten note was lost or an email was overlooked. Manual processes are often messy, and disorganization leads to an endless cycle of time-wasting “catch up.”
An ERP system puts all this information in one centralized place, ensuring that everything you need is easily accessible and trackable. Instead of wasting time looking for information, you’ll know exactly where to find it—whether it’s inventory levels, shipping status, or order history.
This means that you save your own valuable time, and you can put it to use somewhere that really needs your human touch.
Errors: The High Price of Disconnected Processes
One of the biggest dangers of manual processes is their potential for error. When you rely on handwritten notes, disjointed spreadsheets, and manual tracking, there are endless opportunities for something to go wrong.
Maybe someone wrote down the wrong SKU, or maybe a paper got lost. Or maybe someone misinterpreted the scribbled note next to that product. Whatever the error is, it results in miscommunication, delays, and possibly even lost customers.
Errors like these are preventable, and they’re a lot more common than you’d think. And unfortunately, the more manual your processes, the more frequent they become. Every mistake costs you time, money, and credibility.
ERP systems significantly reduce these errors by automating processes and ensuring accurate, real-time data is shared across your entire operation. With an ERP system, you can streamline operations and improve data accuracy, fostering a more connected and efficient environment.
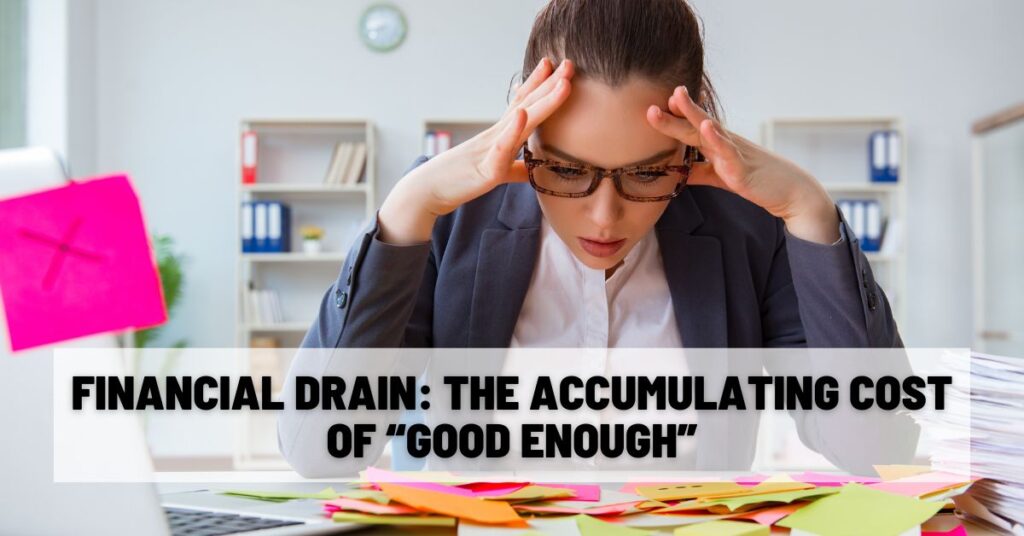
Financial Drain: The Accumulating Cost of “Good Enough”
It’s tempting to stick with what works—if those Post-Its and manual processes have gotten you this far, why change? But that “good enough” approach is probably costing you more than you realize.
For example, manual inventory tracking often leads to overstocking or understocking. One minute, you’re sitting on a warehouse full of excess product, tying up capital in items that aren’t moving. The next minute, you’re scrambling because you’re out of stock on a hot-selling item, and now you’re losing sales. Either way, your money is on the line.
The real cost of these manual systems is the inefficiency they breed. With an ERP, you can automate inventory tracking, manage orders in real-time, and create reordering thresholds that keep your stock at the perfect level. You can stop the financial drain of disorganization and missed opportunities.
Scalability: The Roadblock to Growth
Manual processes might work for now, but what happens when your business grows? The complexity of managing orders, inventory, and supplier relationships only increases as you expand. You’re going to need to shift to more robust, scalable systems as you take on more customers and products.
Scalability is one of the key benefits of an ERP system. As your business grows, your ERP grows with you. You can handle more SKUs, more orders, and more data without things slipping through the cracks. More importantly, an ERP system allows your entire team to be on the same page, with up-to-date information available to everyone at the same time.
The Bottom Line: It’s Time to Upgrade
It’s easy to fall into the habit of sticking with familiar manual processes—after all, they’ve served you well so far. But as your business grows, the inefficiencies, errors, and financial strain of those “good enough” solutions will start to add up.
An ERP system doesn’t just replace sticky notes and spreadsheets—it fundamentally changes how your business operates. With real-time data, automated processes, and scalability, you can save time, reduce errors, and cut costs.
So, maybe it’s time to stop settling for “good enough” and start investing in a system that’s built to take your business to the next level. If that sounds like what you might need, schedule a 15-minute call to talk about your business with one of our ERP experts.