How an Inventory Control System Can Take You from Chaos to Control During Supply Chain Disruptions
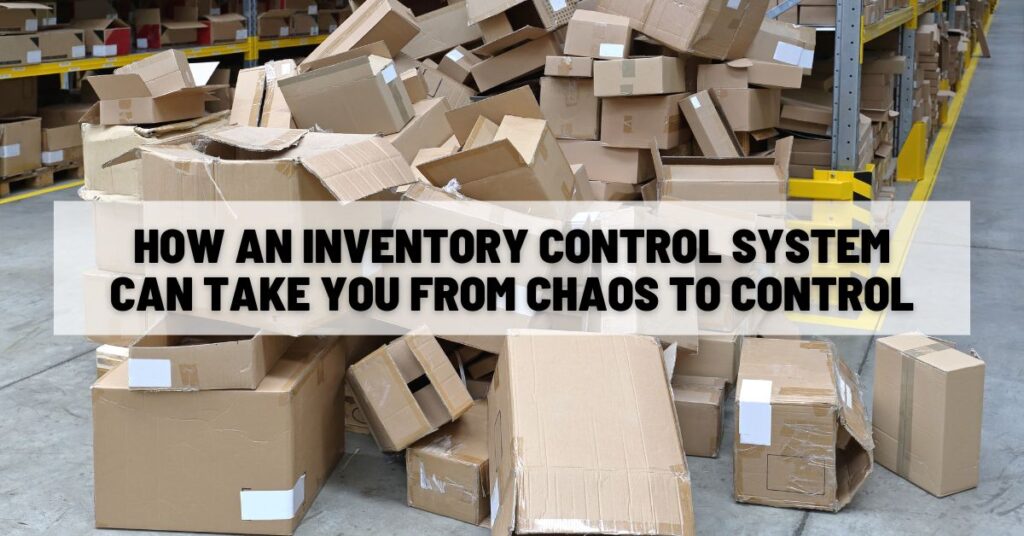
The Chaos of Supply Chain Disruptions
Supply chain disruptions are the peak of chaos for any inventory-centric business. An inventory control system can be the difference between reacting to chaos and proactively managing it.
One delayed shipment, one missed delivery, and suddenly your inventory is out of sync. Orders pile up, shelves go empty, and customer satisfaction takes a nosedive. When your team is forced to spend hours chasing down where components went missing, manually updating records, or negotiating with suppliers in crisis mode, it’s not just stressful—it’s costly.
Let’s look at how these systems can take your inventory from unpredictable to organized, even in challenging times.
Free Inventory Control Guide
What is an Inventory Control System?
An inventory control system is a software solution that centralizes, tracks, and manages your inventory in real time. It gives you a single point of truth for stock levels, orders, and shipments, enabling you to always know exactly what you have and where it is.
Key features include:
- real-time visibility to ensure you can track inventory as it moves,
- automated reordering to help you maintain optimal stock levels without manual intervention, and
- seamless integration with your supply chain partners to keep your entire supply chain connected and efficient.
In an environment where disruptions are the norm, functionality like that is crucial for staying competitive. It lets you respond swiftly to changes in supplier timelines, customer demands, or logistics challenges—turning what could be chaos into a situation you can manage with confidence.
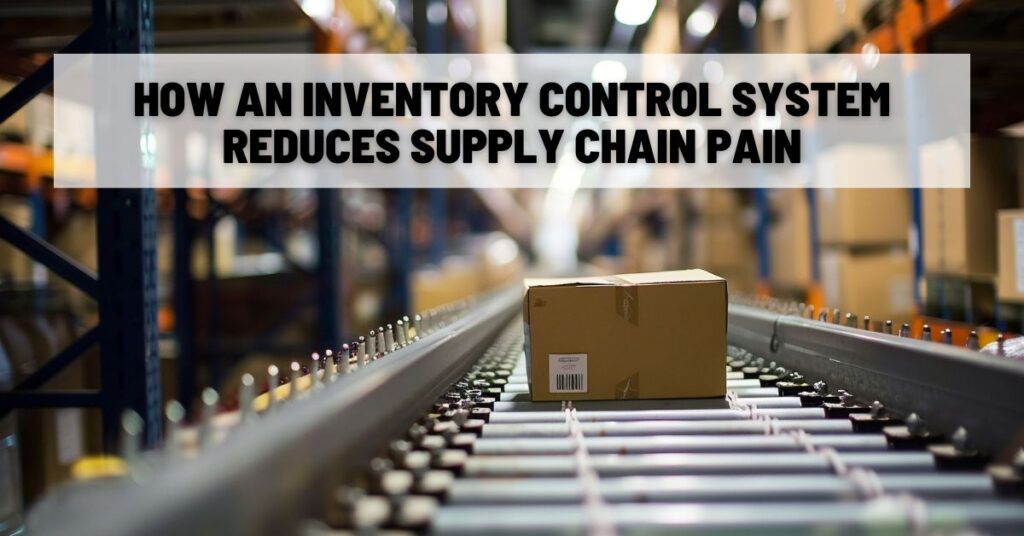
How an Inventory Control System Reduces Supply Chain Pain
Supply chain disruptions can cause chaos, but an inventory control system can turn that uncertainty into a manageable challenge. Here’s a few of the ways how:
Real-Time Inventory Visibility
One of the biggest advantages of an inventory control system is real-time visibility. When disruptions happen—like a delay from a key supplier—knowing exactly what you have in stock allows you to adapt quickly.
Accurate stock levels prevent you from making reactionary, costly mistakes like unnecessary overstock or unexpected shortages. Suppose you run into a delay in raw materials. With real-time data, you can see exactly how much safety stock remains, allowing you to adjust production schedules before it’s too late.
Automated Processes to Reduce Errors
Manual processes, especially during supply chain crises, are prone to human error. An inventory control system automates data entry, order management, and reordering—drastically reducing the chances of mistakes.
For example, automated reordering triggers can prevent stockouts by alerting you when items dip below a pre-set threshold. Automation keeps you from scrambling, ensuring you have what you need, even during unpredictable disruptions.
Scenario Planning and Flexibility
Advanced inventory control systems also allow for proactive planning with scenario analysis. This feature lets you simulate “what if” situations, preparing your team for a range of possible disruptions.
If a supplier delay is detected, for example, the system can trigger an automated alert and suggest alternative sources or reorder adjustments to help you manage the impact. This proactive capability turns unexpected supply chain issues into problems you’re already prepared to solve.
Achieving Control with an Inventory Control System
Supply chain disruptions can make inventory management feel like a constant battle. But with a robust inventory control system, you can transform chaos into clarity. It sounds pretentious, but it’s true.
Moving away from reactionary, manual processes means gaining real-time visibility, automated efficiencies, and the ability to plan for unexpected changes—all key to creating a more resilient, proactive approach to your supply chain.