For U.S.-based industrial supply & equipment manufacturers importing products from overseas, understanding landed cost isn’t just good practice — it’s essential for profitability, pricing accuracy, and operational control. Landed cost represents the total cost of getting a product from your supplier’s door to your warehouse shelf. Without a clear calculation, hidden fees can erode margins and create costly surprises.
Here’s how to properly calculate landed cost — and ensure every shipment supports your bottom line.
What is Landed Cost?
Landed cost is the “all-in” cost of importing goods. It includes not only the purchase price but every expense incurred along the supply chain until the product arrives at your facility, ready for sale or use.
For manufacturers in the industrial supply sector, where margins can be tight and products are often bulky or specialized, accurately calculating landed cost is critical for competitive pricing and financial health.
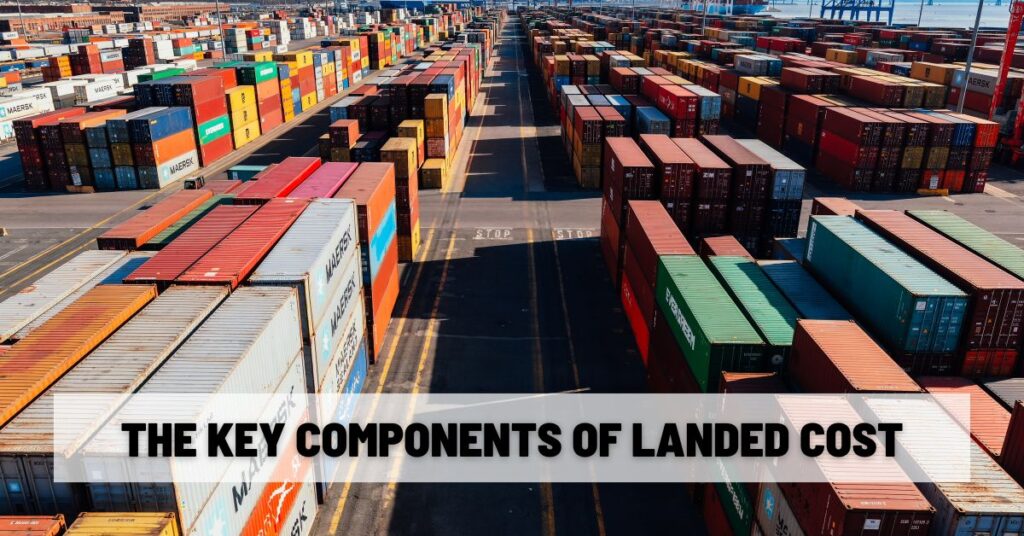
The Key Components of Landed Cost
To calculate landed cost, you need to account for several core elements:
- Product Cost (FOB or EXW Price)
This is the price you pay your overseas supplier. Be clear whether this is FOB (Free on Board) or EXW (Ex Works), as this determines when you assume responsibility for shipping costs. - International Freight Charges
Costs for transporting goods by sea, air, or land from the supplier’s country to the U.S. This includes fuel surcharges, container fees, and terminal handling charges. - Customs Duties and Import Tariffs
The U.S. Customs and Border Protection (CBP) imposes duties based on your product’s HS (Harmonized System) code and country of origin. With ongoing trade tensions, especially with countries like China, tariffs can fluctuate—sometimes significantly. - Customs Brokerage Fees
Brokers handle the complex paperwork and clearance process at U.S. ports. Their service fees should be factored into every shipment. - Insurance
Cargo insurance protects against damage, loss, or theft during transit. This is especially important for high-value industrial equipment. - Port and Handling Fees
These include charges for unloading, storage, and inspection at the port of entry. - Inland Transportation
The cost of moving goods from the port to your warehouse or final destination within the U.S. - Miscellaneous Fees
This could include compliance costs, inspection fees, demurrage (if your shipment is delayed at port), or currency conversion fees.
Landed Cost Formula
A simplified formula for landed cost looks like this:
Landed Cost = Product Cost + Freight + Duties & Tariffs + Insurance + Brokerage + Handling Fees + Inland Transportation + Miscellaneous Costs
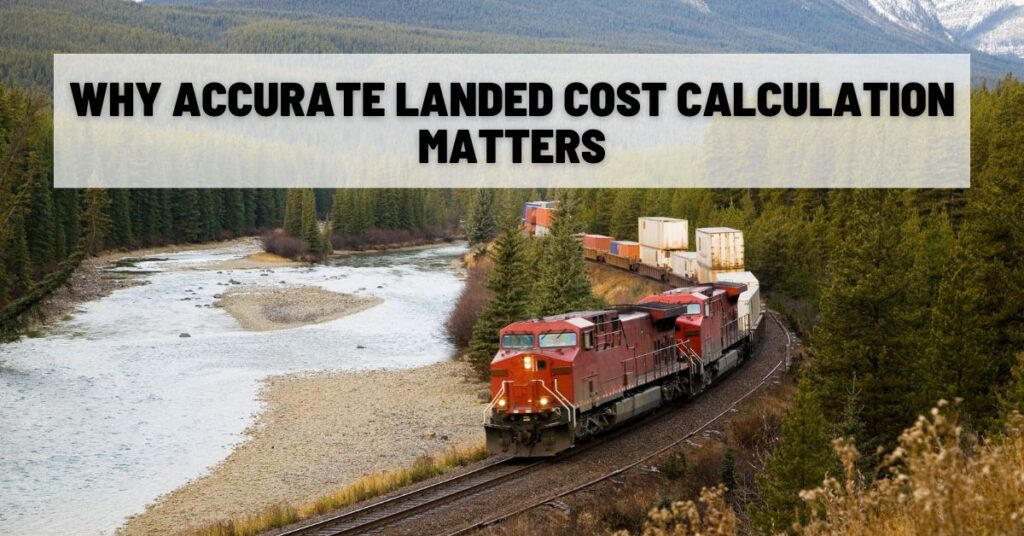
Why Accurate Landed Cost Calculation Matters
For industrial supply manufacturers, miscalculating landed cost can lead to:
- Underpricing products and losing profit.
- Overpricing and becoming uncompetitive.
- Cash flow issues due to unexpected fees at customs.
- Delays in delivery if duties aren’t prepaid.
In today’s dynamic trade environment, especially with tariffs impacted by global trade disputes, staying proactive is crucial.
Best Practices
- Use Landed Cost Software such as AcctVantage ERP: Automate calculations and stay updated on tariff changes.
- Work with Experienced Brokers: They can help classify products correctly and avoid overpaying duties.
- Monitor Trade Policies: Stay informed about new tariffs or trade agreements that could impact costs.
Knowing your true landed cost isn’t optional—it’s the foundation of smart importing and sustainable profitability.